From automotive to aerospace, sheet metal parts are integral components, and any deformation in these parts can lead to significant issues in assembly and functionality. Ensuring the integrity and precision of bent metal pieces is crucial for maintaining the quality and performance of the final product.
To eliminate deformation during the bending process, achieve flawless results, and reduce waste, explore how to avoid deforming bent sheet metal parts. Whether you’re a seasoned professional or just starting out, understanding these key principles will enhance your work and efficiency in handling sheet metal.
Select Suitable Materials
Choosing the right materials sets the foundation for avoiding deformation in bent sheet metal parts. Metals such as aluminum and stainless steel are ideal due to their malleability and strength. However, it’s crucial to match the material properties with the intended application.
For instance, softer metals are easier to bend but might not provide the necessary durability for high-stress environments. On the other hand, harder metals can withstand more strain but are more prone to cracking if not handled correctly. Evaluating factors like tensile strength, yield strength, and ductility will ensure that you select materials capable of achieving precise bends without compromising structural integrity.
Check for Residual Stress
Residual stress can be a silent saboteur in the bending process, leading to unexpected deformations that compromise the quality of your sheet metal parts. Before you even begin bending, it’s essential to identify and address any pre-existing stresses within the material.
This can be done by conducting stress-relief operations such as annealing, which involves heating the metal to a specific temperature and then allowing it to cool slowly. Additionally, using modern tools like X-ray diffraction and ultrasonic stress measurement can help detect and quantify residual stresses, giving you the information needed to take corrective measures.
Perform Pre-Bend Annealing
As mentioned, annealing involves heating the sheet metal to a specific temperature to reduce its hardness and increase its ductility. This makes the metal more pliable and far less likely to crack or deform when bent.
The process typically involves heating the metal in a controlled environment, such as a furnace, to a temperature that’s sufficient to relieve internal stresses. Once at the desired temperature, the metal is then allowed to cool gradually, often in the furnace or in still air. This slow cooling process is essential for achieving a uniform grain structure, which translates to smoother, more consistent bends.
Maintain Proper Bend Radius
The bend radius, which is the inside radius of the bend, plays a pivotal role in preventing cracks, material fatigue, and other issues. A too-tight radius can push the material past its breaking point, resulting in a compromised part.
To achieve the optimal bend radius, always adhere to the recommended minimum bend radius for the specific material being used. Utilizing tools such as adjustable bending dies and dedicated radius gauges can help ensure consistency and precision.
Moreover, taking the time to run preliminary tests on scrap material can provide valuable insights into how the metal behaves during bending. These trial runs allow you to fine-tune your process without risking valuable production material.
Control Bending Speed
Imagine trying to sculpt a clay pot on a wheel that’s spinning too fast or too slow—either way, you’re likely to end up with a misshapen creation. Similarly, if you bend metal too quickly, you might cause unnecessary strain that leads to cracks or warping. On the other hand, bending too slowly can result in material fatigue and an inefficient workflow.
Striking the perfect balance is key. For most materials, a controlled, moderate bending speed ensures that the metal flows into the desired shape without overstressing it. Additionally, keep an eye on environmental factors such as temperature, which can affect bending speed requirements.
Ensure Uniform Thickness
Consistency in the thickness of your sheet metal is paramount to achieving flawless bends and avoiding deformation. To ensure uniform thickness, start by sourcing high-quality materials with guaranteed thickness tolerances. Investing in reliable suppliers and conducting regular quality checks can save you from headaches down the line. Moreover, if your stock materials are not uniformly thick, consider using a thickness planer or other conditioning methods to achieve consistency before the bending process begins.
In addition, always use precision measurement tools, such as micrometers and calipers, to double-check the thickness at multiple points along the sheet. These tools provide the accuracy you need to catch any inconsistencies that might compromise your bends.
Apply Back Tension
Back tension involves adding a counterforce to the metal as it bends, effectively balancing the stresses and ensuring a cleaner, crisper angle. Imagine pulling a rubber band in opposite directions to get it perfectly straight—back tension achieves something similar, preventing the metal from wrinkling or shifting out of place. To implement this, you can use specially designed fixtures or multitasking machinery that allows for simultaneous pulling and bending.
Using back tension doesn’t just prevent deformations but also improves precision, making your bends look sharp and professional. Think of it as having an extra pair of hands guiding the metal into place.
Invest in Quality Machines
The best way to avoid deforming bent sheet metal parts is to invest in quality machines. Whether it’s press brakes, bending dies, or measuring tools, opting for premium equipment ensures reliability and precision. High-quality tools and machines can handle the strains of metal bending, offering consistent performance and reducing the likelihood of unexpected breakdowns. Your investment will also pay off in the form of smoother operations and less material waste.
However, simply buying quality tools isn’t enough—they need your care and attention to keep performing at peak levels. This means you need to schedule routine checks to inspect for wear and tear, ensure moving parts are well-lubricated, and immediately address any issues that arise.
Moreover, keeping your tools clean and properly stored can help extend their lifespan. Dust and debris can cause significant damage over time, so a little housekeeping can go a long way. Consider setting up a dedicated maintenance schedule and training your team on the importance of tool and machine care. Not only will this save you money in the long run, but it will also enhance the quality of your work.
If you’re in need of a high-quality machine that will help you achieve precise bends even on your most delicate materials, Mac-Tech has the steel folding machine for you. The Stefa long folding machine is the epitome of modern metal folding technology, offering consistent, exact results.
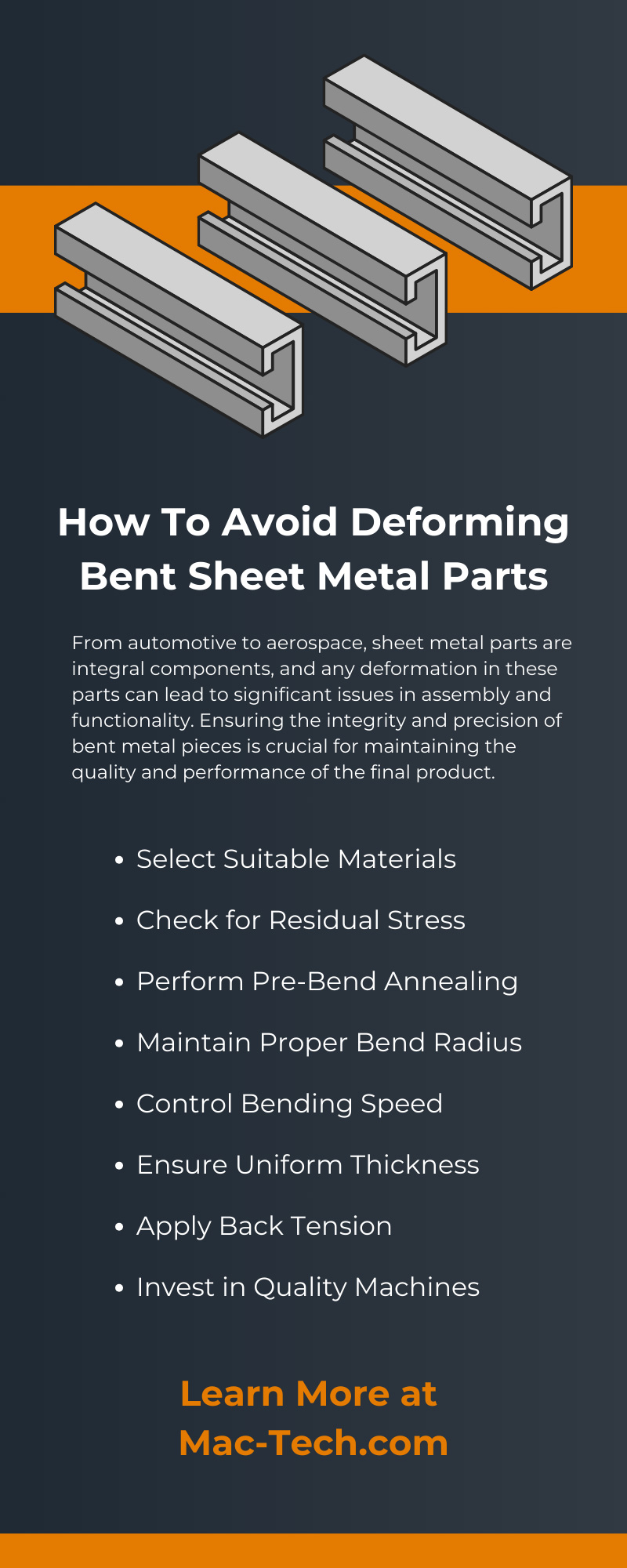
Get Weekly Mac-Tech News & Updates